Carbon Capture and Storage
Holcim is committed to decarbonising building for a net-zero future
How we’re planning to decarbonise our Cauldon cement operations
Cement is an essential material to help us build the schools, homes, offices and infrastructure the UK needs, as well as being critical to the country’s economy.
We’ve been producing cement from our Cauldon plant in Staffordshire since 1957, today employing more than 140 people directly, as well as providing ongoing work for hundreds of specialist contractors.
Within our cement business, we’ve already made great strides in lowering the carbon content of a number of products - our ECOplanet range for example has up to 30 per cent less embodied carbon, made possible by using an alternative material GGBS.
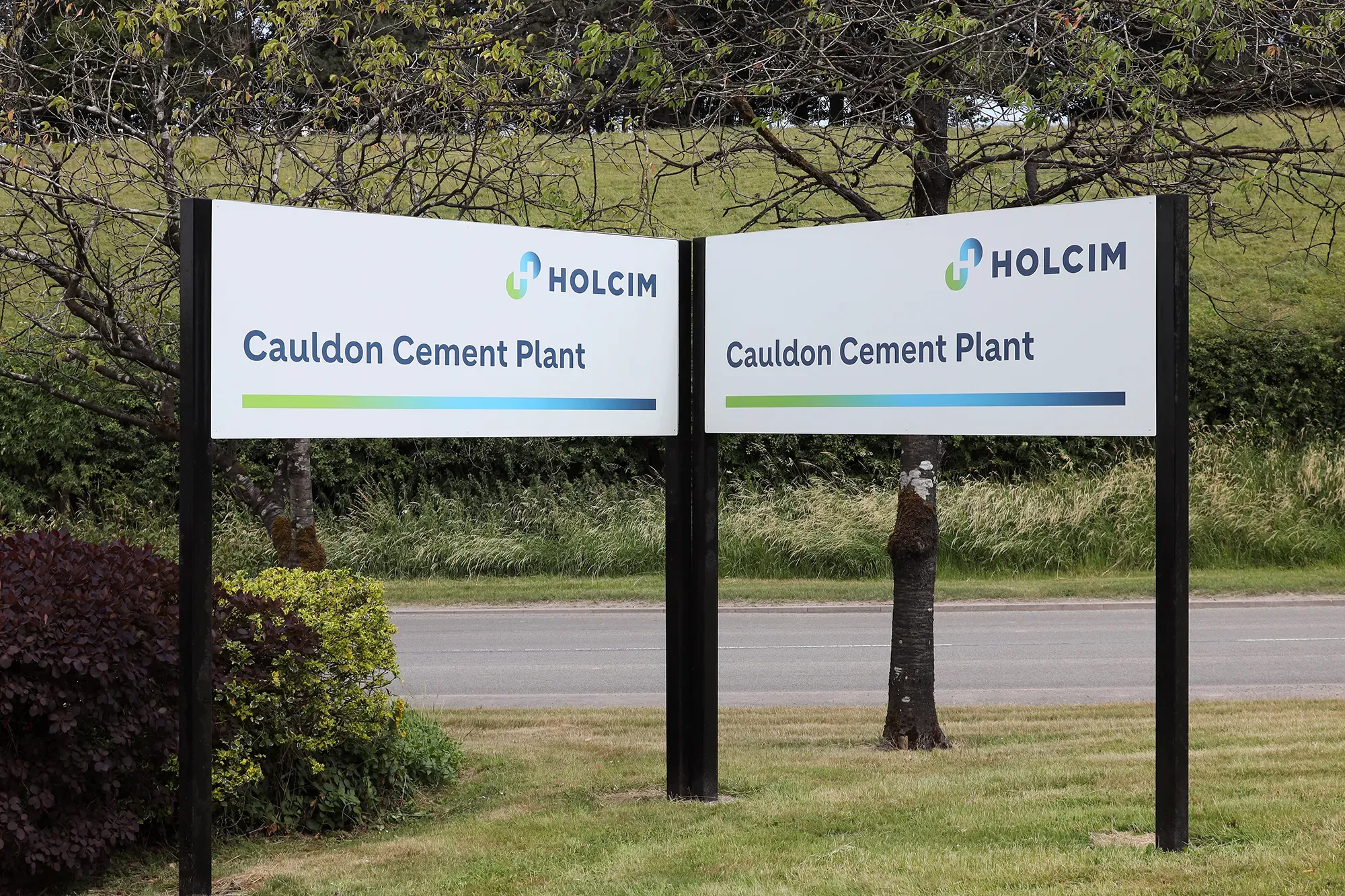
But to truly decarbonise and to help produce as near to net zero cement as possible the only viable option is to implement carbon, capture and storage technology. This has been tried and tested in the oil and gas industry for many years.
It will require building a capture plant that sits at the heart of our wider Cauldon masterplan. We’ll continue to reduce carbon through the use of alternative fuels, alternative raw materials, greener logistics solutions plus the renewable energy options being explored on site. Any remaining carbon will be captured by our new facility at source, before being safely transported and stored.
Why Carbon Capture and Storage?
We have committed to achieving net zero across our operations by 2050. Decarbonising our cement manufacturing process is key to that.
The way cement is manufactured - by heating limestone to extremely high temperatures - triggers a chemical reaction which includes the emissions of carbon dioxide. This process results in 70 per cent of our overall CO2 emissions as a company.
Cement remains a hugely essential material to the way we build and construct so we must aim to decarbonise not deindustrialise.
We have made great strides in lowering our carbon emissions through the use of alternative fuels, energy efficiency and the use of alternative materials but ultimately these measures will only take us so far on our net zero journey.
Carbon capture allows us to capture the CO2 at source and transport it safely via an established pipeline to be securely stored.